جوشکاری
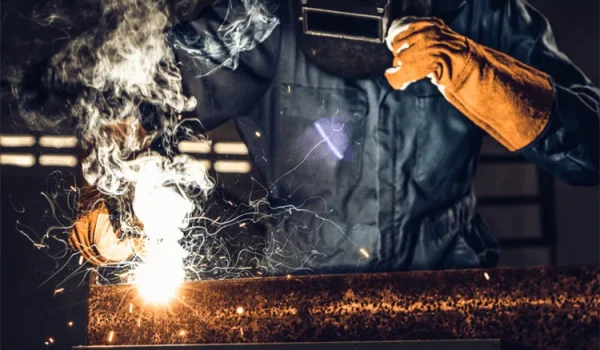
جوشکاری
جوشکاری به فرآیند اتصال فلزات ، سرامیک، پلاستیک و … به وسیله اعمال فشار یا گرما و یا همزمان اطلاق میگردد. در اینجا بحث اتصال فلزات پایه توسط منبع انرژی به فلز همگن یا غیر همگن می باشد.جوشکاری به روش های دستی SMAW ، جوشکاری زیر پودری ، جوشکاری GMAW و جوشکاری تنگستن TIG از متداولترین نوع جوشکاری در صنعت می باشد. با توجه به نوع اتصال ،نوع فلز پایه و الکترود مصرفی دستورالعمل اجرایی جوش که به WPS معروف است توسط مهندسین جوش تهیه و جهت اجرا به جوشکار مجرب در این زمینه ارائه می گردد.کیفیت جوش مستلزم رعایت نکات فراوانی از قبیل دستگاه رکتیفایر یا ترانسفورماتور های کالیبره و استاندارد ،جوشکار ماهر،ابزار مناسب ( الکارود ، انبر ، کابل و…) و اماده سازی اولیه سطح میباشد.رعایت آمپر ، ولتاژ ، زاویه و سرعت جوشکاری توسط جوشکار الزامی بوده و این امر در جوشهای نفوذی از اهمیت بالایی برخوردار میباشد.
جوشکاری چیست؟
یکی از روشهای ساخت میباشد که هدف آن اتصال دائمی مواد مهندسی از قبیل فلز، سرامیک، پلیمر و کامپوزیت بهیکدیگر است؛ و این کار معمولاً از طریق ایجاد حرارت بالا و ذوب ماده و سپس سرد کردن برای ایجاد جوش انجام میشود. جوشکاری با روشهای اتصال دما پایینتری مانند لحیمکاری نرم (Soldering) و لحیمکاری سخت (Brazing) که در آنها فلز پایه ذوب نمیشود، تفاوت دارد.
در جوشکاری علاوه بر ذوب فلز پایه، معمولاً از یک ماده به عنوان پرکننده نقطه اتصال (Filler) استفاده میشود تا حوضچه ای از مواد مذاب ایجاد گردد که پس از خنک شدن و ایجاد اتصال میتواند از فلز یا ماده پایه نیز قوی تر باشد. همچنین ممکن است از فشار در کنار گرما یا به تنهایی برای تولید جوش استفاده گردد. ضمناً در جوشکاری به نوعی محافظ برای حفاظت از فلزات پرکننده یا فلزات ذوب شده در برابر اکسید شدن یا آلودگی نیاز است.
برای ایجاد حرارت مورد نیاز جوشکاری از منابع انرژی متعددی میتوان استفاده کرد، از قبیل: شعله گاز، قوس الکتریکی، لیزر، پرتوی الکترون، اصطکاک، و امواج مافوق صوت. همچنین جوشکاری در محیطهای صنعتی مختلفی قابل اجراست از قبیل: هوای آزاد، جوشکاری زیر آب، و خارج از اتمسفر زمین. جوشکاری یک کار خطرناک است و برای جلوگیری از سوختگی، شوک الکتریکی، آسیب چشمی و دید، استنشاق گازهای سمی و دود و قرار گرفتن در معرض اشعه ماوراء بنفش شدید، نیاز به احتیاط میباشد.
فرایندهای جوشکاری
فرایندهای جوشکاری با قوس الکتریکی
۱- پوشش ۲- الکترود ۳- گاز محافظ ۴- جوش ۵- فلز پایه ۶- فلز جوش داده شده ۷- انجماد گِل جوش
جریان الکتریکی از جاریشدن الکترونها در یک مسیر هادی بهوجود میآید. هرگاه در مسیر مذکور یک شکاف هوا (گاز) ایجاد شود، جریان الکترونی و در نتیجه جریان الکتریکی قطع خواهد شد. چنانچه شکاف هوا بهاندازهٔ کافی باریک بوده و اختلاف پتانسیل و شدت جریان بالا، گاز میان شکاف یونیزهشده و قوس الکتریکی برقرار میشود. از قوس الکتریکی بهعنوان منبع حرارتی در جوشکاری استفاده میشود. حرارت ایجاد شده در جوشکاری به دلیل حرکت الکترونها در ستون قوس و بمباران الکترونی قطعه کار میباشد. روشهای جوشکاری با قوس الکتریکی عبارتاند از:
• جوشکاری با الکترود دستی پوششدار (Shielded Metal Arc Welding-SMAW)
• جوشکاری زیرپودری (submerged arc welding-SAW)
• جوشکاری با گاز محافظ (GMAW یا MIG/MAG)
• جوشکاری با گاز محافظ و الکترود تنگستنی (GTAW یا جوشکاری TIG)
• جوشکاری پلاسما
فرایندهای جوشکاری مقاومتی
یک دستگاه جوش نقطه ای. نوک بازوهای مسی در سمت چپ محل قرار گرفتن دو قطعه و ایجاد اتصال است.
در جوشکاری مقاومتی با عبور یک جریان الکتریکی بالا از درون قطعه کار، و ایجاد گرما به دلیل وجود مقاومت الکتریکی و فشار وارد شده از سمت بازوهای مسی اتصال ایجاد میگردد. با عبور جریان زیاد (۱۰۰۰ تا ۱۰۰۰۰ آمپر) از درون فلز، حوضچه کوچکی از فلز مذاب در منطقه جوش ایجاد میشود. بهطور کلی، روشهای جوشکاری مقاومتی کارآمد هستند و آلودگی کمی ایجاد میکنند، اما کاربرد آنها تا حدودی محدود است و هزینه تجهیزات میتواند زیاد باشد.روشهای جوشکاری مقاومتی عبارتند از:
• جوش نقطهای
• درز جوش
• جوش تکمهای
• با استفاده از قالب
فرایندهای جوشکاری حالت جامد
دستهای از فرایندهای جوشکاری هستند که در آنها عمل جوشکاری بدون ذوبشدن لبهها انجام میشود. در واقع لبههای تحت فشار با حرارت یا بدون حرارت در همدیگر له میشوند. فرایندهای این گروه عبارتاند از:
• جوشکاری اصطکاکی: در این روش بهجای استفاده از انرژی الکتریکی برای تولید گرمای مورد نیاز ذوب فلزات از انرژی مکانیکی استفاده میگردد. بهاین ترتیب که یکی از دو قطعه که با سرعت درحال دوران است بهقطعهٔ دوم که ثابت نگه داشتهشده تماس داده میشود. در اثر اصطکاک بین دو قطعه و تولید حرارت، محل تماس دو قطعه ذوبشده و لبههای تحت فشار با حرارت در همدیگر له میشوند.
• جوشکاری نفوذی
• جوشکاری با امواج مافوق صوت
فرایند جوشکاری با گاز
جوشکاری با گاز یکی از گروه فرایندهای جوشکاری است که در آن، اتصال با ذوبشدن توسط یک یا چند شعله مانند استیلن یا پروپان، با اعمال فشار یا بدون آن، با کاربرد فلز پرکننده یا بدون آن انجام میشود.
از لیزرهای مختلفی مانند «زر گاز کربنیکی» یا لیزر یاقوت برای جوشکاری میتوان استفاده کرد. دقت میشود که انرژی پرتو، آنقدر زیاد نباشد که باعث تبخیر فلز شود.
جوشکاری با اشعه الکترونی
کاربرد جریانی از الکترونها است که با ولتاژ زیاد شتاب داده شدهاند و بهصورت باریکهای متمرکز بهعنوان منبع حرارتی جوشکاری بهکار میروند. بهدلیل چگالی بالای انرژی در این پرتو، منطقه تفدیده بسیار باریک میباشد و جوشی با کیفیت مناسب بهدست میآید. این فرایند بهعنوان اولین فرایند جوشکاری بهکاررفته برای ساخت بدنهٔ جنگندهها استفاده شد
اثرات گرما
متالورژی جوشکاری
گرمایش و سرمایش از مولفههای اصلی اکثر فرایندهای جوشکاری است. این گرمایش و سرمایش معمولاً اثرات نامطلوبی بر روی متالورژی مواد دارد. در جوشکاری ذوبی، گرما به حدی است که میتواند مقداری از فلز پایه را ذوب کرده (ماده ای که در حال جوشکاری است)، و در ادامه معمولاً یک خنک کاری سریع اتفاق میافتد. اثرات حرارتی برای این نوع جوشکاری بسیار بارز است، اما در فرایندهایی که گرمایش-سرمایش با سرعت و شیب کمتری اتفاق میافتد کمتر است. اگر به اثرات حرارتی به حد کافی توجه شود، معمولاً میتوان این اثرات نامطلوب را کاملاً از بین برده یا آن را به حداقل رساند، و به جوشی با کارایی فوقالعاده دست پیدا کرد.
از آنجایی که حوضچه مذاب معمولاً نسبت به قطعه اصلی کوچک است، جوشکاری ذوبی را میتوان به عنوان “یک قطعه ریختگی کوچک در داخل یک قالب بزرگ” در نظر گرفت. خواص و ترکیب ماده نهایی حوضچه جوش، مخلوطی است از ماده مادر و الکترود یا سیم جوش. نسبت این مواد بستگی به عواملی از قبیل نوع فرایند جوشکاری، شکل اتصال، و آمادهسازی لبه قطعات دارد.
از آنجایی که ترکیب شیمیایی این ناحیه و فرایند ذوب و انجماد آن با باقی فلز مادر متفاوت است، نمیتوان انتظار داشت که خواص آن با فلز اصلی یکسان باشد. در نتیجه برای دستیابی به خواص مکانیکی مطلوب باید فیلر یا الکترودی انتخاب شود که خواص آن در حالت «پس از ذوب و انجماد» برابر یا بالاتر از فلز مادر باشد. به همین دلیل در بسیاری از موارد ترکیب شیمیایی الکترود یا فیلر کمی با فلز مادر متفاوت است. ساختار دانهها در ناحیه ذوب شده میتواند ریز یا درشت، هم محور (equiaxed) یا ریشه درختی (dendritic)، باشد و این بستگی به نوع و حجم فلز جوشکاری و نرخ خنک کاری دارد، اما ترکیب شیمیایی اکثر الکترودها و سیم جوشها تمایل دارند دانههایی ریز و هم محور تولید کنند. برابری یا بالاتر بودن استحکام الکترودها و سیم جوشها از فلز مادر در حالت پس از جوشکاری، مبنای بسیاری از استانداردها و مشخصات فنی تعیین شده توسط AWS (انجمن جوشکاری آمریکا) است.
حوضچه فلز مذاب ایجاد شده در اثر جوشکاری ذوبی مستعد همه مشکلات و نقایص مربوط به ریختهگری فلزات، مانند تخلخل گاز، ناخالصیها، حفره گاز، ترک و انقباض است. از آنجا که معمولاً مقدار فلز مذاب در مقایسه با جرم کل قطعه کار کم است و فلز اطراف آن رسانش گرمایی خوبی دارد، انجماد و خنک سازی سریع فلز نیز کاملاً رایج است. از نقایص مرتبط با این شرایط نیز میتوان به دام انداختن گازهای محلول (تخلخل گازی)، تفکیک شیمیایی، تغییر اندازه دانه، مشکلات شکل دانه و اثرات جهتگیری اشاره کرد.
منطقه متأثر از گرما
جوشکاری پاس ریشه یک لوله. ناحیه تغییر رنگ داده شده که به وضوح مشخص است، «ناحیه متأثر از گرما» است. در اکثر اتصالهای جوشی، ناحیه متأثر از گرما یا HAZ ضعیفترین قسمت جوش میباشد.
در مجاورت حوضچه مذاب و کاملاً در داخل فلز پایه، تقریباً همیشه، ناحیه یا منطقه ای تحت عنوان منطقه متأثر از گرما به انگلیسی: (heat affected zone) وجود دارد. در این ناحیه، که معمولاً به اختصار HAZ خوانده میشود، فلز مادر ذوب نشده، اما برای مدت زمانی کوتاه دمای آن بسیار بالا رفتهاست. فلز مجاور ممکن است حرارت کافی برای تغییر در ساختار و خواص از قبیل: تبدیل فاز، تبلور مجدد، رشد دانه، رسوب یا درشت سازی رسوبی، تردی یا حتی ترک خوردگی، جذب کرده باشد.
به دلیل ساختار تغییر یافته، ناحیه متأثر از گرما ممکن است دیگر از خواص مطلوب ماده اصلی برخوردار نباشد و از آنجا که ذوب نشدهاست، نمیتوان خواص آن را مشابه حوضچه جامد شده در نظر گرفت. در نتیجه، منطقه متأثر از گرما اغلب ضعیفترین منطقه در اتصال جوشی است. به جز در مواردی که نقص آشکاری در حوضچه جامد شده وجود دارد، بیشتر شکستهای جوشکاری در منطقه متأثر از گرما ایجاد میگردد.
معمولاً اگر خواص ایجاد شده پس از جوشکاری مطلوب نباشد، خواص و ساختار کل سازه جوشکاری شده توسط عملیات حرارتی اصلاح میگردد.
قابلیت جوشکاری یا اتصال
همه مواد مهندسی قابلیت جوشکاری توسط هر نوع فرایند جوشکاری را ندارند. هر چند که این مقیاس تقریباً مبهم است، اما معمولاً از عبارت “قابلیت جوشکاری” یا “قابلیت اتصال” برای تعیین امکان جوشکاری یک ماده در اتصال توسط جوشکاری استفاده میشوند. استفاده از یک فرایند جوشکاری میتواند نتایج فوقالعاده ای بدست دهد، در حالیکه استفاده از فرایندی دیگر ممکن است باعث یک اتصال ضعیف شود. تغییر پارامترهایی از قبیل نوع ماده الکترود، گاز محافظ، سرعت جوشکاری و نرخ خنک کاری میتواند کیفیت یک فرایند را بشدت تغییر دهد.
فرآیند جوشکاری قوسی با الکترود دستی (Shielded Metal Arc Welding)
در اصطلاح عامیانه به آن جوش برق یا جوشکاری SMAW هم میگویند. (در صنعت، نام عامیانهی جوش برق به جوشکاری الکترود دستی و جوش گاز به جوشکاری اکسی استیلن اطلاق میشود)
فرایند جوشکاری برق، زیر مجموعهای از جوشکاری با انرژی الکتریکی و جوش کاری قوسی با محافظت سرباره است.
بیشترین کاربرد جوشکاری در صنعت کشور ما از کارگاههای کوچک تا کاربردهای آن در واحدهای بزرگ صنعتی مربوط به این روش است. در گذشته جوشکاری با سیم فلزی لخت انجام میشد. اما پس از مدتی، ساخت الکترودهای پوشش دار جهت سهولت در جوشکاری با کیفیت بهتر مطرح شد.
صنعتگری سوئدی بنام اسکار جلبرگ، با فرو بردن سیم آهنی در ترکیب غلیظی از کربنات و سیلیکات و سپس خنک کردن آن، الکترود فلزی پوشش دار را اختراع نمود. به همین دلیل بحث پوشش الکترود مطرح شد و ترکیبات پوشش اهمیت یافت.
مزایای جوشکاری با قوسی با الکترود دستی
• محدودیت انواع حالات جوشکاری و محدودیت فضا و مکان در این روش وجود ندارد.
• میتوانیم در کارگاه یا در محل دور افتاده بیابانی حتی این فرایند را انجام دهیم فقط کافیست دستگاه جوشکاری را عوض کنیم.
• از قدرت مانور زیاد برای جوشکار حتی در طراحی قطعات با زوایای تنگ و بسته و جاهایی که دسترسی به محل جوش مشکل است، وجود دارد.
• جوشکاری الکترود دستی نسبتا ارزان است.
محدودیتها
• کیفیت جوش به مهارت جوشکار بستگی دارد.
• مسئله تعویض الکترود علاوه بر تاخیر زیادی که در حین کار بوجود میآورد، کیفیت جوش را از نظر یکنواختی زیر سوال میبرد. – بحث تمیز کردن سرباره و محبوس شدن آن در بخشهای داخلی جوش وجود دارد.
• برای تمام فلزات و آلیاژها، الکترود مناسب آنها را نداریم. به عنوان مثال برای جوشکاری تیتانیوم و منیزیم و آلیاژهای آن، الکترود متناسب وجود ندارد.
• در برابر وزش باد حساس است.
• محدودیت ضخامت قطعه نیز وجود دارد.
دستگاه جوش : (power source)
در این فرایند از هر چهار نوع مولد نیرو (دستگاه جوشکاری) یعنی ترانسفورماتور، رکتیفایر، دینام و موتور جوش استفاده میشود. محدوده جریان این فرآیند بین ۵۰ تا ۳۰۰ آمپر است و در موارد خیلی خاص و برای الکترودهای خیلی باریک نیاز به دستگاهی با جریان زیر ۵۰ آمپر داریم. نکته دیگری که در اینجا مطرح است سیکل تناوب است که در کاتالوگ دستگاه درج میشود.
وسایل کمکی:
وسایلی از قبیل کابل، گیره، انبر، برس، پیشبند، ماسک و غیره نیز اهمیت دارد. به عنوان مثال ماسک، یک شیشه تار بوده و جلوی بخشی از امواج مضر برای چشم و پوست را میگیرد و بر اساس نوع الکترود، میزان آمپر و نوع فرآیند درجه تاری آن تغییر کرده و معمولاً به صورت نمره بیان میشود.
الکترود:
الکترودها به طور کلی از دو بخش هسته و پوشش تشکیل شده که هسته معمولاً فلزی و پوشش از مواد سرامیکی ساخته شده و بر اساس نوع پوشش به چند دسته تقسیم میشوند که می توان به الکترودهای سلولزی، روتیلی، روتیل قلیایی، اکسیدی، اسیدی و قلیایی اشاره کرد.
استانداردهای الکترود جوشکاری:
استاندارد الکترودهای جوشکاری در کلاس های استاندارد آلمان (DIN)، ژاپن (JIS)، اروپا (EN)، امریکا (AWS) و استاندارد بین المللی (ISO) تقسیم بندی میشوند. استاندارد زیر مثالی از نحوه خوانش اینگونه استانداردها است.
زاویه الکترود جوشکاری:
در انجام عملیات جوشکاری مواردی وجود دارد که از عیوب جوشکاری هستند این موارد یا باید حذف شوند و به حداقل رسانده شوند. یکی از مواردی که لازم است در کاهش این عیوب رعایت کرد زاویه ی صحیح نگهداشتن الکترود است.
انجام جوشکاری با زاویه صحیح باعث ایجاد جوش هایی می شود که از کیفیت بهتر و میزان عیوب کمتر برخوردار هستند. از عیوبی که در اثر نبود صحیح زاویه الکترود به وجود می آید می توان به این موارد اشاره کرد: ناخالصی سرباره (Slag Inclusion)، ذوب ناقص (Lack of Fusion)، نفوذ ناقص (Lack of penetration) و حبس سرباره، تخلخل و یا بریدگی کناره جوش.
با در نظر گرفتن پخ جوش و وضعیت کار برای کنترل کیفیت بهتر جوشکاری جهت گیری الکترود از اهمیت بالایی برخوردار است. وضعیت و موقعیت مناسب الکترود وابسته به موارد از جمله شکل هندسی اتصال، موقعیت جوشکاری، اندازه و نوع الکترود است. مهارت یک جوشکار باعث می شود که در هنگام جوشکاری همه این موارد را در نظر بگیرد. در تعیین جهت گیری الکترود از دو عامل زاویه حرکت و زاویه کار استفاده می شود.
زاویه حرکت:
زاویه بین سطح الکترود و سطح کار را گویند که کمتر از ۹۰ درجه است.
زمانیکه الکترود در مسیر جوشکاری قرار دارد از روش جوشکاری پیش دستی استفاده می شود. به این خاطر به زاویه حرکت، زاویه فشار هم گفته می شود.
زمانیکه الکترود بر خلاف جهت مسیر جوشکاری حرکت کند به این تکنیک جوشکاری پس دستی گفته می شود و به زاویه حرکت در این حالت، زاویه کشیدن می گویند.
زاویه کار:
زاویه کار زاویه ای است بین یک خط عمود بر سطح قطعه کار اصلی و صفحاتی که به وسیله ی محور الکترود و محور جوش تعیین می شود و این زاویه نیز کمتر از ۹۰ درجه است.
معایب و مزایای زوایه صحیح الکترود
اعمال کنترل خوب روی حوضچه جوش مذاب، ذوب کامل فلز پایه و نفوذ مطلوب از مزایای موقعیت صحیح الکترود است.
اما در زمان هایی که زاویه حرکت الکترود بزرگ باشد باعث ایجاد معایبی همچون بد شکل شدن ، نفوذ ناکافی و همچنین ایجاد درز در جوش مقعر خواهد شد. از معایب زاویه حرکت کوچک می توان به تجمع سرباره اشاره کرد. در مورد عدم زاویه کار مناسب نیز می توان گفت زمانیکه زاویه کار بزرگ باشد امکان سوختن کناره جوش وجود دارد و هنگامی که زاویه کار کوچک باشد ذوب بطور ناقص تشکیل خواهد شد.
جوشکاری زیر پودری (Submerged Arc Welding)
در جوشکاری زیرپودری یا جوشکاری SAW، فلز الکترود و مواد روانساز از یکدیگر جدا هستند. از یک کلاف سیم توپر استفاده شده و توسط قرقرههایی به سمت پایین و به طرف محل جوش حرکت داده میشود. کل مجموعه از داخل نازلی که به جریان الکتریکی متصل است عبور میکند.
در این نوع جوشکاری، به منظور حذف فرایند تعویض الکترود، الکترود، بدون پوشش بوده و جایی که نیاز به پوشش است، از فلاکس داخل یک مخزن استفاده میشود.
در اثر حرارت قوس، بخشی از پودر فلاکس که روی کار ریخته شده است ذوب میشود. سپس سیم و قطعه کار هم ذوب شده و به این ترتیب عملیات جوشکاری انجام میشود. پوشیده شدن حوضچهی مذاب با این دانههای ریز و پودرها، موجب حفاظت حوضچه از طریق ایجاد یک سرباره میشود. این فرایند، جوشکاری قوس مخفی نیز نام دارد.
تجهیزات جوشکاری SAW
ماشین جوش (مولد نیرو از نوع ترانس و یا رکتیفایر) و سیستمهای کنترلکننده، تجهیزات اصلی این فرایند هستند.
سیستمهای کنترلکننده شامل:
• سیستمهای الکترونیکی: از جمله سیستمهای تنظیم کننده آمپر، ولتاژ، سرعت راندن سیم و سرعت جوشکاری است.
• سیستمهای مکانیکی: از جمله تنظیم کنندهی مسیر جوشکاری و مقدار اضافه شدن پودر محافظ میباشد.
مزایا
• فرایند، بهطور کلی ماشینی و اتوماتیک است. این مسئله چندین مزیت دارد :
• عوامل وابسته به جوشکار از جمله مهارت و کاهش کیفیت کار ناشی از خستگی فردی از بین میرود.
• بحث تعویض الکترود همانطور که قبلا گفتیم در این روش حذف شده است و این خود باعث ایجاد یکنواختی جوش، هم از نظر ظاهری و هم از نظر کیفیت شده و سرعت کار نیز بهطور محسوسی بالا میرود.
• با توجه به اینکه قوس مخفی است، مضرات ناشی از عوارض نور قوس برای چشم و پوست حذف میشود. علاوه بر این حساسیت جوش کاری در برابر وزش باد نیز ناچیز است.
محدودیتها
• مخفی بودن قوس که باعث عدم بررسی و مشاهده لحظهای جوش کار از مسیر و روند جوشکاری میشود.
• محدودیت در وضعیت جوشکاری با توجه به ماهیت فرایند و عدم استفاده از این روش برای جوشکاریهای قائم و بالای سر
• بالا بودن هزینه تمامشده تجهیزات و دستگاهها که البته بعضا میتواند مزیت و گاها محدودیت محسوب شود.
عمده کاربردها
از فرآيند جوش كاري قوس زيرپودري بيشتر براي جوشكاري صنعتی قطعات ضخيم، خط جوشهاي طويل مثل صنايع لولهسازي، کشتیسازی، جوشکاری اسکلتهای فلزی و ساخت مخازن استفاده میشود. یکی از کاربردهای متداول جوشکاری زیرپودری در ساخت لوله است.
جوش کاری قوس با گاز محافظ (Gas Metal Arc Welding)
در فرآيند جوش کاری قوسي با الکترود مصرفی تحت پوشش گاز محافظ، از الکترود بدون پوشش استفاده شده و براي محافظت از حوضچهی مذاب جوشکاری، از یک گاز كم اثر يا بی اثر در فضاي قوس و اطراف حوضچه مذاب استفاده میشود. گاز محافظ از طريق كپسول و لولههاي انتقال به آرامي به اطراف قوس هدايت شده و حفاظت مناسب را ايجاد ميكند.
در اين فرآيند که با نام جوشکاری GMAW نیز شناخته میشود، چنانچه از گاز محافظ خنثي يا بی اثر از جمله گاز آرگون یا هليوم استفاده شود (بهخصوص برای فلزاتی که در مقابل اتمسفر حساسیت بالایی دارند از جمله آلومینیوم و فولاد زنگ نزن) به آن جوشکاری MIG (میگ) میگویند و جوشکاری MAG (مگ) نام همین فرایند است اگر از گاز نيمه فعال مانند CO2 استفاده شود. بنابراین جوشکاری co2 زیرمجموعه جوشکاری MAG محسوب میشود.
تجهیزات
تجهیزات کلی و جانبی این فرایند نیز مانند فرایندهای قبلی جوشکاری قوسی است با این تفاوت که نیاز به یک سیستم تامین گاز محافظ نیز داریم. گاز محافظ از کپسول به كمك رگلاتور و شیلنگ به مشعل جوشکاری منتقل می شود.
دبی سنج، شلنگ هدایتکننده و یک هیتر به منظور تبدیل CO2 مایع درون کپسول به گاز، از سایر تجهیزات سیستم تامینکننده گاز محسوب میشود. علاوه بر این موارد نیز به یک سیستم خنککننده (مبرد) که میتواند هوا باشد یا سیستمی شبیه به رادیاتور ماشین و استفاده از آب به منظور خنک کردن محل جوشکاری، نیاز است. مجموعهی نگهدارندهی الکترود، سیستم خنککننده، نازل ترموستات و گاز محافظ در مشعل تفنگی(Gun torch) قرار دارد.
مزایا
• محدودیت مربوط به حالت های جوشکاری، تعویض الکترود و تمیز کردن سرباره وجود ندارد.
• دامنهی کاربرد وسیع است و برای انواع فلزات و آلیاژها را می توان از این روش بهره برد. برای مثال برای جوشکاری آلومینیوم، تیتانیوم و منیزیم باید از روش جوشکاری MIG استفاده کرد.
محدودیتها
از عیوب این روش می توان به گران بودن تجهیزات آن، حساسیت بالا به وزش باد و همچنین سریع سرد شدن منطقه حوضچه مذاب اشاره کرد.
عمده کاربردها
اين نوع جوشكاري بهدليل تداوم جوشكاري و عدم توقف ناشي از تعويض الكترود به صورت اتومات و با استفاده از رباتها در صنايع مختلف مثل: اتومبيلسازي، واگنسازي، كشتیسازي و ساير سازههاي فلزي كاربرد وسيعي دارد.
فرآیند جوش کاری قوس با الکترود تنگستن و گاز خنثی (Tungsten Inert Gas)
این فرایند با عنوان جوشکاری آرگون یا جوشکاری تیگ نیز معروف است. باید گفت که این یک غلط رایج است. چون در آن میتوان از گاز هلیم یا مخلوطی از هلیم و آرگون نیز استفاده کرد. این فرایند معمولا برای جوشکاریهای حساس که کیفیت بالایی مدنظر است مورد استفاده قرار میگیرد.
جوشکاری TIG یکی ديگر از فرایندهای جوشکاری قوسی است كه در آن قوس بين الكترود غيرمصرفي ديرذوب تنگستن و قطعه كار برقرار میگردد و باعث ذوب فلز پايه و ايجاد حوضچه مذاب روي قطعه كار میشود.
تجهیزات دقیقا مشابه روش جوشکاری میگ بوده با این تفاوت که الکترود مورد استفاده، الکترود غیرمصرفی دیرذوب تنگستن میباشد.
مزایای جوشکاری TIG
• جوشکاری ارگون بصورت هر سه نوع دستی، نیمه اتوماتیک و اتوماتیک قابل انجام است.
• فرایندی نسبتا تمیز است؛ به این معنا که هم دود و سربارهای وجود ندارد، و همچنین فلز جوش عاری از هرگونه ناخالصی و آخال است چرا که در اینجا هیچ ترکیبی بین گاز و مذاب وجود ندارد و محافظت بهخوبی انجام شده و ترکیب آلیاژی نهایی جوش کاملا کنترل شده است.
• از دیگر مزایای این فرایند، تمرکز حرارت بالا و دمای بالای قوس است که باعث افزایش کاربرد برای فلزات با هدایت حرارتی بالا میشود.
• استقلال منبع حرارتی از فلز پرکننده و بالعکس نیز موجب تغییر میزان رسوب در نقاط مختلف جوش میشود.
محدودیت های جوشکاری TIG
گران بودن تجهیزات و دستگاهها، بحث مسائل ایمنی بصورت شدیدتر و حساسیت بالا در برابر جریان باد از محدودیتهای این روش جوشکاری است.
عمده کاربرها
صنایع موشکی و کاربردهای نظامی و تعمیرات برخی نیروگاهها، جوشکاری آلومینیوم، مس، تیتانیوم، منیزیم و فولادهای زنگ نزن، کاربردهای مربوط به صنایع غذا و دارو که کیفیت و حساسیت بالا مد نظر است.
جوشكاري اكسي استيلن(Oxy-Fuel Gas Welding)
جوشکاری اکسی استیلن یکی از متداولترین انواع فرایندهای جوش کاری در صنعت ایران محسوب میشود و در بین جوشکارهای سنتی به نام جوش کاربید یا جوشکاری کاربیت نیز شناخته میشود. این فرایند، از نظر تعداد واحدهایی که از آن استفاده میکنند در رتبه دوم و از نظر حجم و تناژ تولید محصولات با این روش در رتبه چهارم یا پنجم قرار دارد، چون این روش بیشتر مورد استفاده برای کاربردهای ظریف است.
جوشكاري اكسی استيلن فرآیندی است که از انرژی حرارتی ناشی از سوختن یک گاز سوختنی مثل استیلن
برای ذوب کردن درز اتصال و سیم جوش فلزی بدون روپوش استفاده میشود. در كپسولها، گاز اکسیژن و استیلن به صورت فشرده وجود دارد. فشار گازها توسط رگلاتورها کاهش یافته و تنظیم میشود و از طریق دو شیلنگ لاستیکی به طرف مشعل هدایت میشوند.
علاوه بر سه راهی و رگلاتور، شیر یک طرفه نیز در مسير گازها نصب میشود تا مانع از برگشت گاز و شعله به طرف کپسول شود.
فرآیندهای جوشکاری مقاومتی (Electric Resistance Welding)
این دسته از فرایندها که با نام جوشکاری ERW نیز شناخته میشوند، از انرژی الکتریکی (البته بدون وجود قوس الکتریکی) استفاده میکنند. در این فرایند، جریان الکتریکی از یک مقاومت عبور میکند و بر اساس قوانین الکتریکی، حرارت ایجاد شده موضع مورد نظر را گرم و خمیری و حتی ذوب کرده و عمل جوشکاری انجام میشود. در واقع اتصال دو سطح در اثر حرارت ناشي از اعمال جریان الکتریکي و فشار مکانیکي بهصورت همزمان ایجاد ميشود.
بالا بودن مقاومت الکتریکي و عبور جریان الکتریسیته در محل تماس دو سطح، بر اساس قوانین الکتریکی، حرارت ایجاد میکند. با این کار، موضع مورد نظر را گرم، خمیری و حتی ذوب شده و عمل جوشکاری انجام میشود. سپس فشار لازم نیز از طریق الکترودها به محل اتصال وارد میشود و فصل مشترك که در اثر عبور جریان برق با آمپر زیاد خمیری شده را در هم ادغام میکند.
اجراي جوشکاري مقاومتی از سرعت بالایي برخوردار است و در این فرآیند از ماده مصرفي مثل سیم جوش
یا الکترود مصرفي استفاده نميشود. همچنین فرآیند جوشکاري مقاومتی از قابلیت اتوماسیون بالایي برخوردار است.
تجهیزات مورد نیاز جوشکاری ERW
ترانس و الکترود دو بخش اصلی این فرایند محسوب میشود و همچون فرایندهای پیشین، مواد مصرفی نداریم.
مزایا
• راندمان بالا به دلیل تمرکز حرارتی بالا علیرغم وجود شعله و گرمای خارجی
• عدم وجود مواد مصرفی
• ایمنی بالا و نبود مشکلاتی در رابطه با اشعه، برق گرفتگی و مشکلات تنفسی
محدودیتها
• در این فرآیند جوشکاری، محدودیت بیشینه ضخامت مطرح است و تنها مناسب قطعات با ضخامت کمتر از ۵ میلیمتر ست.
• جنس فلز قطعه کار نیز اهمیت دارد و برای فلزاتی که ویژگیهای زیر را دارند این روش مناسب نیست:
1. مقاومت الکتریکی پایینی دارند، از جمله آلومینیوم.
2. خاصیت سختیپذیری بالایی دارند مثل فولاد پر کربن و فولاد آلیاژی.
3. دارای پوشش است.
عمده کاربردها
براي جوشکاري ورقهاي بسیار نازك و متوسط عملکرد خوبي دارد.
فرآیند جوش کاري مقاومتي در صنایع خودروسازي، کابینتسازي و لوازم خانگي کاربرد وسیعي دارد.
انواع اتصالات جوشی
اتصال لببهلب (Butt Joint)
از این نوع اتصال، عموماً به منظور متصل کردن انتهای ورقهای مسطح با ضخامتهای تقریباً یکسان استفاده میشود. مزیت اتصال لببهلب، جلوگیری از خروج از مرکزیتی است که در اتصالات روی هم یکطرفه مطابق با شکل قبل ایجاد میگردد اگر در اتصالات لببهلب از جوش شیاری با نفوذ کامل بهره گرفته شود، اندازه اتصال به کمترین مقدار خود رسیده و شکل ظاهری آن هم بسیار مطلوبتر از دیگر اتصالات میگردد.
اتصال سپری (Tee Joint)
کاربرد اتصال سپری غالباً در ساخت نیمرخهای مرکب به شکل T و I، سختکنندههای تحت بار، تیرورقها، آویزها، قطعاتی که با زاویه باهم جفت میشوند و همچنین نشیمنهای طاقچهای میباشد.
اتصال پیشانی (Edge Joint)
این مدل اتصال، اصولاً نقش سازهای بر عهده ندارد و کاربرد آنها صرفاً در نگهداری دو یا چند صفحه در یک سطح و یا نگهداری امتداد اولیه عضو میباشد.
اتصال گونیا (Corner Joint)
کاربرد اتصا گونیا عمدتاً در ساخت مقاطع جعبهای به شکل مستطیل است که تیرها و ستونهای مقاوم در برابر پیچش را تشکیل میدهند.
نمونه اتصال گونیا
اتصال روی هم یا پوششی (Lap Joint)
روش اتصال روی هم، متداولترین روش اتصال است و دارای دو مزیت عمده میباشد:
• سهولت در جفت و جو کردن: برخلاف روشهای دیگر، ساختن قطعات در این نوع اتصال به زمان زیادی نیاز ندارد. همچنین در اتصال پوششی قطعات میتوانند اندکی روی هم جابهجا شوند تا ایرادهای کوچک ساخت را پوشانده یا تنظیم طول را ممکن سازند.
• سهولت در اتصال دادن: در این نوع اتصال، نیازی به آمادگی خاص لبههای قطعات متصل شونده نیست و غالباً آنها یا با شعله یا به صورت عادی برش میخورند. در اتصال روی هم عمدتاً از جوش گوشه استفاده میشود.
انواع جوش
جوشهای شیاری
کاربرد اصلی جوش شیاری در اتصال دادن قطعات سازهای است که در امتداد هم و در روی یک سطح واقع شدهاند. چون جوشهای شیاری عمدتاً بری انتقال کل نیروی قطعاتی که توسط این جوش اتصال مییابند مود استفاده قرار میگیرد، بنابراین لازم است تا جوش دارای مقاومتی هم اندازه با مقاومت قطعات اتصال یافته باشند. این مدل جوش شیاری را جوش شیاری با نفوذ کامل مینامند. زمانی که درز جوش بهگونهای طراحی گردد که جوش شیاری در تمام عمق قطعات اتصال یافته پخش نشود، جوش شیاری را جوش شیاری با نفوذ نسبی میگویند. در طراحی این مدل جوشها باید نکات مهم و خاصی را مدنظر قرار داد. در اغلب جوشهای شیاری، لبه درز جوش به شکل خاصی آمادهسازی میگردد. نامگذاری انواع درز جوش نیز با دقت به این به موضوع، صورت گرفته است.
انواع رایج درز جوشکاری
عواملی همچون روند جوشکاری مورد استفاده، هزینهی آمادهسازی لبهی درزهای جوش و همچنین هزینه عملیات جوشکاری نقش مهمی در انتخاب جوش شیاری مناسب دارند.
علاوه بر این در ساخت اتصالات سپری نیز میتوان از جوش شیاری استفاده کرد.
جوش گوشه
کاربرد جوش گوشه نسبت به دیگر جوشها بیشتر است زیرا علاوه بر اقتصادی بودن، استفاده از آن هم راحت است و همچنین میتواند در عمده موارد جوشکاری بهکار روند.
در این نوع جوش به دلیل روی هم گرفتن قطعات، نیازی چندانی به دقت در جفت و جور کردن نیست، در حالی که در جوش شیاری لازم است که قطعات را با دقت زیاد در یک امتداد قرار داد و شکافی در ریشهی جوش میان آنها باقی گذاشت. جوش گوشه دارای مزیتهای زیادی است مخصوصاً برای جوشکاری در محل نصب و یا برای جفت کردن مجدد اعضا یا اتصالاتی که از قبل با رواداریهای مناسبی ساخته شدهاند.
جزییات جوش گوشه
جوشهای کام و انگشتانه
این دو مدل جوش را میتوان به تنهایی یا به صورت مخلوط با جوش گوشه، استفاده کرد. از جمله موارد استفاده از جوش کام و انگشتانه، انتقال برش در اتصالات پوششی میباشد در زمانی که طول جوش گوشه یا دیگر انواع جوش پاسخگو نیست. علاوه بر این، جوشهای مذکور به منظور مقابله با کمانش قسمتهای روی هم گذاشته نیز به کار میرود.